Improving Material Bonding and Joining Quality
The trend towards lightweighting and increased usage of composite materials presents new challenges in material bonding and joining technologies. Traditional joining methods, such as riveting and screwing, introduce damage to the composite structure and generally are not preferred. Therefore, joining methods such as bonding with adhesives and welding that doesn’t damage the laminate are being refined and becoming popular.
Thermoplastic Welding Control
An important innovation is the use of induction welding to join composite materials based on a thermoplastic polymer. With this process, an induction coil creates eddy currents which heats the polymer to the point of melting. The two parts are then pressed together, forming a strong and cohesive bond.
HD-FOS temperature sensors can be directly embedded within the welded joint to obtain in-situ temperature measurements along the length of the joint throughout the entire welding process
Temperature control is a major challenge when employing thermoplastic welding. A common practice to control and move the induction coil at a constant fixed travel rate, which can lead to variations in the material temperature and inconsistent bonding. However, HD-FOS temperature sensors can be directly embedded within the welded joint to obtain in-situ temperature measurements along the length of the joint throughout the entire welding process, resulting in better welds, reduced waste and reduced development time.
In-Situ Bond Measurements
Because high-definition fiber optic sensing (HD-FOS) uses very low profile fiber (155 μm), HD-FOS sensors can be embedded in the bond or weld line without affecting the strength or reliability of the bond. Embedded HD-FOS strain sensors can provide in-situ strain measurements which can be used to indicate the quality and durability of the bond, and even indicate any areas of debonding.
Featured Products
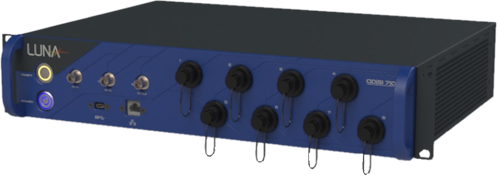
High-Definition Distributed Fiber Optic Sensing
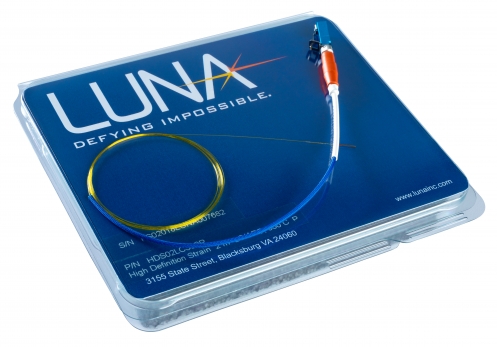