FEM/FEA Model Validation
Finite element modeling and finite element analysis (FEM/FEA) is widely used in the design of structural components and systems. Since FEA models include assumptions and simplifications, access to experimental data is critical to verify and adjust the model to assure a higher level of accuracy.
The use of composite materials and structures increases the need for verification and validation due to their inhomogeneity and complications such as the fiber/matrix interaction, fiber geometry, and interfacial bonding. In addition to the complex nature of these materials, there are many variables in the manufacturing process that cannot be accounted for in the model.
HD-FOS provides accurate strain data along the length of a very small fiber, even along complex geometries.
The traditional approach to model validation and calibration is the use of resistance foil strain gages. However, foil gages only provide discrete measurement locations and do not provide the detail needed for composite structures. On the other hand, high-definition fiber optic sensing (HD-FOS) provides accurate strain data along the length of a very small fiber, even along complex geometries.
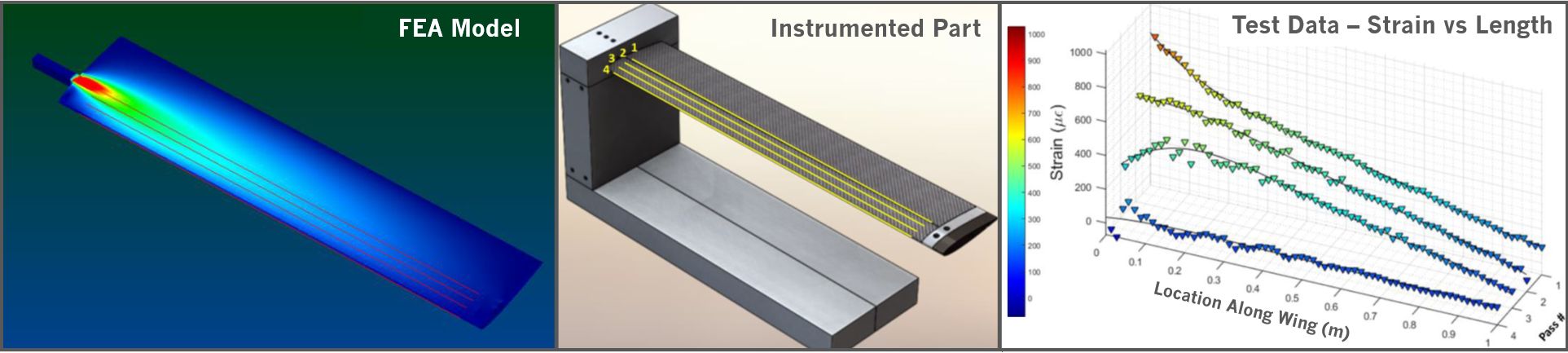
When model validation requires dynamic sensor data, involves very large structures or requires onboard testing, Luna’s high-speed multipoint sensing solution, based on fiber Bragg grating (FBG) and Fabry-Perot technology, provides high-performance discrete sensing with all the benefits of fiber optic sensing. HD-FOS provides accurate strain data along the length of a very small fiber, even along complex geometries.
Featured Products
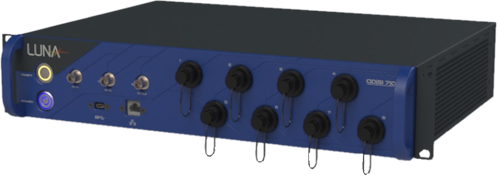
High-Definition Distributed Fiber Optic Sensing
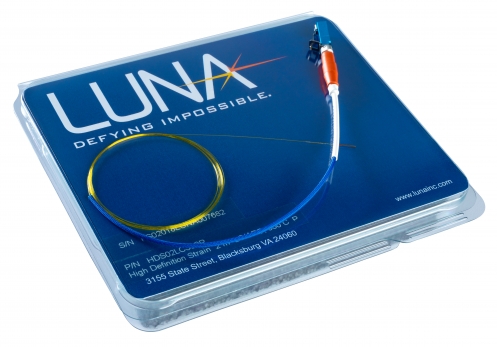
High-Definition Sensors
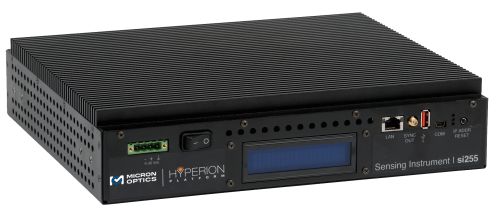