What if you Could Monitor your Additive Manufacturing Process In Situ?
A recent presentation at the Additive Manufacturing Users Group explored how Luna Innovations and Fabrisonic have been been collaborating on 3D printed “smart structures” to answer this question. A joint team is working with the Defense Logistics Agency to create a smart baseplate capable of measuring strain and temperature during a Powder Bed Fusion (PBF) build.
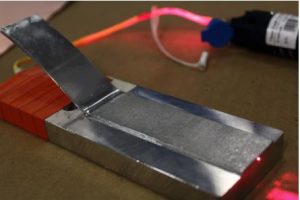
Ultrasonic Additive Manufacturing (UAM), a solid state metal 3D printing technology that occurs at very low temperatures, was used to print metal plates with embedded fiber optic sensors. These specialized sensors can be used to measure strain and temperature anywhere along the length of a single fiber. The combination of solid state 3D printing and High Definition Fiber Optic Sensing (HD-FOS) is being used to create smart baseplates for PBF machines.
Under this program, the team has embedded a matrix of sensor fibers into the top .080" of PBF baseplates. These instrumented plates were placed into a PBF machine as the starting point of a powder build. The PBF team was able collect hundreds of strain and temperature data points in real time during the build. The goal of this project is to improve methodology for PBF processes by learning to anticipate potential issues and to calibrate process models.