High-Definition Fiber Optic Sensing for Rocket Propulsion Testing
Risks inherent with spaceflight necessitate a ground testing regime for rocket propulsion systems that is comprehensive and of very high fidelity. Luna’s high-definition fiber optic sensing instrument (ODiSI) was conceptually demonstrated as a feasible supplement for traditional instrumentation to monitor locations that are both hazardous and otherwise inaccessible. Along with our partner, Fabrisonic LLC, Luna Innovations recently demonstrated SensePipe.
SensePipe combines high-definition fiber optic sensors that are embedded into a section of piping using Ultrasonic Additive Manufacturing technology. SensePipe is a drop-in pipe section that is able to measure multiple parameters including distributed temperature, pressure, strain, and heat flux allowing engineers to better understand fluid flow and the structural health of the piping system.
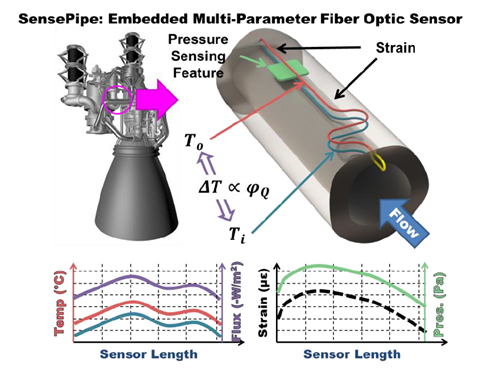
Ultrasonic Additive Manufacturing is a process that builds up solid metal objects through ultrasonically welding a succession of metal foils into a three- dimensional shape. UAM is compatible with many different metals including various aluminum alloys, coppers, steels, and more. Three SensePipe prototypes were constructed from 6061-T6 Aluminum with two high-definition fiber optic sensors embedded in each specimen. Fiber optic sensors were interrogated using Luna Innovations’ proprietary optical frequency domain reflectometry (OFDR) method to directly measure both temperature and strain every 0.65mm along the length of the sensor. With each sensor measuring thousands of points, the technology provides the most complete picture of the temperature and strain within the piping section of any viable sensing technique.
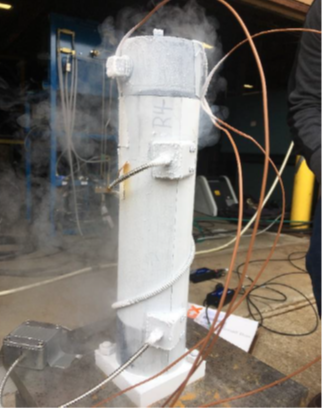
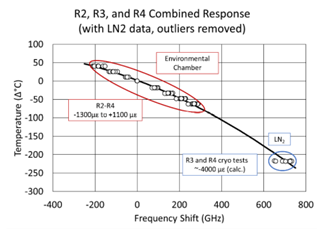
The SensePipe design accounted for the location and layout of the fiber optic sensor in the pipe wall to directly measure inner and outer temperature, axial strain, and hoop strain. From these values, local pressure and heat flux can be derived. Testing to demonstrate the feasibility of using strain and temeprature responses of the system to derive pressure and heat flux were conducted in a laboratory setting. The prototypes were used to measure pressure up to 20.7 MPa, temperatures from -191°C to 70°C and derive heat flux measurements to 6 (105) W/m2.
The use of SensePipe in the application of Rocket Propulsion Testing has numerous advantages. Traditional instrumentation requires extensive wiring that is bulky and arduous to manage in the field. Wiring is also susceptible to induced currents from electromagnetic interference thereby potentially compromising the measurement accuracy. By incorporating multiple measurements into a single set of optical fiber sensors, testing infrastructure can be reduced by a significant amount. SensePipe successfully demonstrated the ability to embed fiber optic sensors within metal parts fabricated using UAM. In addition to Rocket Propulsion Testing, SensePipe has since been adapted to other process piping applications. To learn more about SensePipe or Luna Innovations high-definition fiber optic sensing technology please contact us at [email protected].
Acknowledgments:
- The authors would like to thank NASA for funding this research through a Phase I STTR (contract #80NSSC18P2125)
References:
- Boulanger, A.J., Kominsky D., Hehr A., Herbert P., “Embedded Fiber Optic Sensors for Multi-Parameter Fluid Measurements”, NASA Phase 1 STTR Contract #80NSSC18P2125