Enabling Electrified Aircraft With Fiber
Electric aviation has emerged as a potential solution to reduce greenhouse gas emissions and address resource depletion in the aviation industry. Testing and characterizing electric motors for aircraft applications is crucial to realize the full potential of electric aviation. Luna teamed with partner magniX, a leading manufacturer of Electric Propulsion Units (EPU’s), to demonstrate the efficacy of fiber optic measurements for electric propulsion unit testing. The results were presented at the AIAA Electric Aircraft Technologies Symposium (EATS).
The study highlights the advantages of fiber optic sensors, such as the ability to accurately measure temperature in the presence of strong electromagnetic interference. In the paper, the experimental setups for both dynamometer and propeller test rigs are described along with the results from testing. During the full power tests thorough EMI measurements were performed in proximity to the electric motor. This collection of datasets helped researchers to understand and analyze the frequency content that the fiber optic instrumentation was exposed to in the context of the environment.
The team obtained temperature measurements using fiber optic sensors coupled with Luna’s HYPERION system. The findings demonstrate the effectiveness of fiber optic sensors in a high-power electric motor environment and their potential contribution to the advancement of electric aviation.
A photo from the propeller test rig demonstration is shown below. This facility consisted of the EPU mounted in a structure which encapsulates all the components needed for ground testing including the propeller, governor, and auxiliary components. The magni650 is powered by five DC power supplies with an output shaft driving a five-blade constant speed propeller.
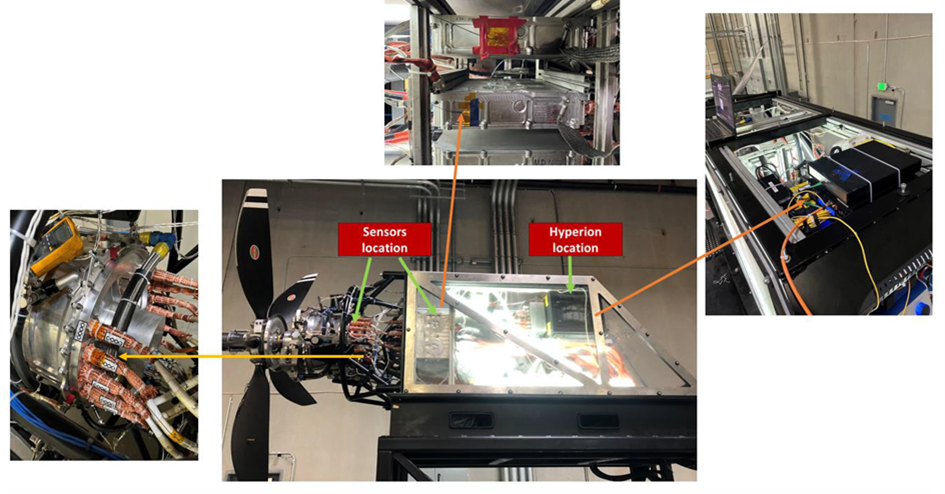
Fiber optic temperature sensors were installed on the outer part of the phase cables going into the motor and the inverter casing while the HYPERION was mounted and secured to the metal frame. The HYPERION reported accurate temperature data during the entire test, including at full speed and maximum power. The measured temperatures track roughly with motor RPM and power consumed. Sharp decreases in temperature can be observed at lower speeds and power levels, which is likely due to cooling from the significant airflow still present even at low speeds around the motor.
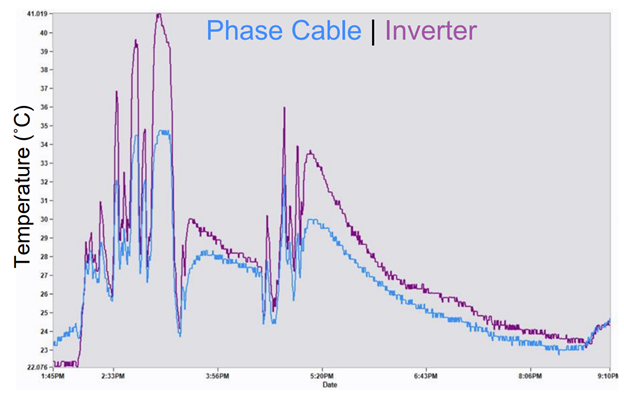
Temperature measurements play a crucial role in ensuring the safe and reliable operation of electric aviation, as they provide critical information for Health Monitoring systems. Monitoring the temperature of batteries, motor components, high power electronics, and cables is essential for ensuring the safety, reliability, and efficiency of electric motors for aviation applications.
Alternative solutions such as thermocouples, resistance temperature detectors (RTDs), thermistors, and wireless sensors have limiting factors such as complex wiring, EMI susceptibility, added weight, and wireless data transfer reliability. Fiber optic sensors overcome these factors as they are easily embeddable, very lightweight, and immune to EMI.
To learn more about HYPERION or Luna Innovations fiber optic sensing technology please contact us at [email protected].
Acknowledgments:
• The authors would like to thank NASA for funding this research through contract #80NSSC22PB073 issued through the Small Business Innovation Research (SBIR) Program
References:
• Roggia, G., Westcott, C. “Fiber Optic Sensor Measurements on High Power Electric Propulsion Unit for Aerospace Applications”. AIAA AVIATION 2023 Forum 12-16 June 2023 San Diego, CA. Paper Number: AIAA 2023-3994. https://doi.org/10.2514/6.2023-3994