HD-FOS helping to integrate composites into the design and validation frame work for the aerospace industry
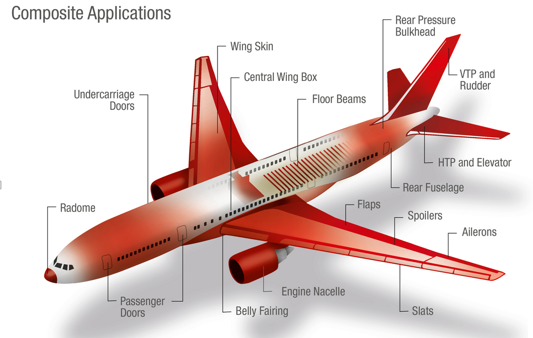
Luna Innovations will be speaking at the September 22nd JEC Forums (Boston) conference, titled “Validating Composite Design using High Definition Fiber Optic Sensing (HD-FOS)”. The presentation specifically targets how HD-FOS can help to advance the integration of composites into the design and validation framework of aircraft production. Composites now make up 50% of the material used in the latest generation of commercial aircraft. With new regulations in place to further improve aircraft efficiency this percentage will only increase. In order for aircraft manufactures to economically scale up in production, without sacrificing quality, both the commercial and military sectors will need to integrate composite materials into their design framework in much the same way as traditional metals. This integration will rely heavily on technologies that integrate new and existing tools for design, manufacturability and design validation. Luna Innovations’ ODiSI product line with HD-FOS technology addresses the growing need for technologically advanced design validation tools. The design goals for aircraft manufactured with composites are essentially the same as those manufactured with traditional metals and are driven by mission profile, load cases and service life. These in turn drive requirements for structural strength, fatigue life and damage tolerance. The use of composites however adds new complexities given the anisotropic and heterogeneous characteristics of composite material. Furthermore, the processes supporting composite manufacturing add higher levels of variability given manufacturing imperfections and inherent variation in the layup process. Variability in the bonding of joints, as well as fastening methods, needs to be considered in the design and validation process. This variability and lack of overall data will result in the need for more testing required at the material, component and final assembly levels. Luna’s ODiSI product platform with HD-FOS offers unique capabilities to support this increased level of design validation testing. The high definition data provides a strain measurement for each millimeter of sensor length and is perfect for validating FE models, particularly those models specifically developed to analyze hot spots or fatigue critical locations (FCL). This high density data is also well suited to measure strain around stress concentration points such as fastener locations or machined areas of the composite part. The ability of HD-FOS to provide a full field view of strain will also be an essential tool in the study of crack initiation and propagation during fatigue testing and will contribute to a more accurate determination of damage tolerance assessment. The sensor is constructed of unaltered fiber optic cable and, at only 155 microns in diameter, can be embedded within composite structures without influencing the parameters under test. This provides aircraft designers an unprecedented level of insight that can help shape design methodology as well as refine manufacturing processes. All of these capabilities will be highlighted in Luna’s JEC Forums presentation through actual examples and case studies. If you’d like to learn more about Luna’s ODiSI product line or HD-FOS in general, then stop by Luna’s booth at the upcoming JEC Forums (Boston) conference. If you can’t make the JEC Forums conference then please request additional information through our website or by responding to this blog. Reference: Kenneth Griffin Ph.D., Keeping U.S. Military Aircraft Flightworthy”, Technology Today Fall 2014