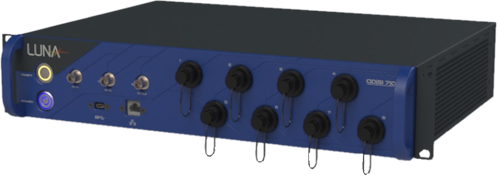
Optical Distributed Sensor Interrogators
The ODiSI 7100 Series is an innovative measurement system specifically designed to address the test challenges of 21st century advanced materials and systems.
Product Description
The ODiSI 7100 Series provides thousands of strain or temperature measurements per meter of a single high-definition fiber sensor. The ultra-high resolution data can fully map the contour of strain for a structure under test or the continuous temperature profile of a process in real time.
The sensor is flexible, low profile, requires no electrical source and can be bonded to sharply curved surfaces, embedded within structures or mounted directly to electrical surfaces.
The ODiSI system captures strain and temperature data with unmatched spatial resolution and precision, delivering valuable benefits for measurement and control applications:
• Capture details not available with conventional point sensors or other fiber optic sensing technologies
• Real-time data from demanding environments and difficult-to-instrument locations